Variable Speed Chillers
Variable Speed Chillers are refrigeration systems equipped with compressors that have variable frequency drives (VFDs). These drives enable the compressor motor to adjust its speed according to the cooling load demand. This capability allows variable speed chiller to operate more efficiently by matching their output to the precise cooling needs, thereby saving energy compared to traditional chillers that operate at fixed speeds. They are particularly advantageous in applications where cooling loads vary throughout the day or seasonally.
VFDs (Variable Speed Chillers)
Types of
Air-Cooled Variable Speed Chillers:
- Definition: Air-cooled variable speed chillers use ambient air as the primary cooling medium to dissipate heat from the refrigerant.
- Description: These chillers typically feature fans that blow air over condenser coils to remove heat. They are suitable for applications where water availability is limited or where water costs are prohibitive.
- Advantages: Lower water consumption, simpler installation without the need for cooling towers or water loops, and reduced maintenance compared to water-cooled systems.
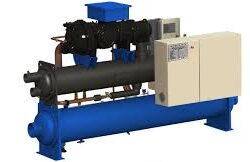
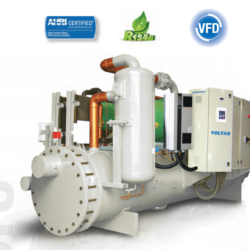
VFDs (Variable Speed Chillers)
Types of
Water-Cooled Variable Speed Chillers:
- Definition: Water-cooled variable speed chillers utilize water as the cooling medium to dissipate heat from the refrigerant.
- Description: These chillers transfer heat to a separate water loop or cooling tower, which dissipates heat into the atmosphere through evaporation or direct contact with air. They are commonly used in larger commercial and industrial settings where higher cooling capacities are required.
- Advantages: Higher efficiency due to superior heat transfer properties of water, suitable for applications with larger cooling loads and continuous operation.
VFDs (Variable Speed Chillers)
Functions
- Compressor with VFD (Variable Frequency Drive):
- Function: Adjusts compressor speed to match cooling demand, optimizing energy efficiency by avoiding constant on/off cycling.
- Condenser Coils:
- Function: Transfers heat from the refrigerant gas to ambient air blown over the coils by fans, cooling the refrigerant.
- Fans:
- Function: Blow ambient air across the condenser coils to facilitate heat dissipation, enhancing overall cooling efficiency.
- Evaporator:
- Function: Absorbs heat from the chilled water or process fluid, lowering its temperature before it returns to the cooling loop.
- Control System:
- Function: Monitors chiller operation adjusts settings in real-time based on cooling needs, and ensures efficient and reliable.
VFDs (Variable Speed Chillers)
Components
- Compressor: Typically centrifugal or screw type, equipped with a VFD for variable speed operation.
- Condenser Coils: Made of materials like copper or aluminum for efficient heat transfer from refrigerant to ambient air.
- Fans: Axial or centrifugal fans that move air across condenser coils to dissipate heat.
- Evaporator: Coils where heat is absorbed from chilled water or fluid, maintaining desired cooling temperatures.
- Expansion Valve: Controls refrigerant flow into the evaporator, regulating system pressure and temperature.
- Variable Frequency Drive (VFD): Adjusts compressor motor speed based on cooling demand, optimizing energy consumption.
- Control System: Includes sensors, controllers, and a user interface to monitor and manage chiller operation effectively.
Other Chiller Products We Manufacture
Air Cooled Chiller
Air-cooled chillers are refrigeration systems that use air to dissipate heat from the coolant or refrigerant. Unlike water-cooled chiller, which rely on a water source and cooling towers
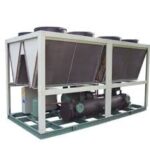
Water Cooled Chiller
Water Cooled Chillers are refrigeration systems that use water as a cooling medium to transfer heat away from the refrigerant. They are widely used in large-scale industrial
Screw Chiller
Screw Chillers are a type of refrigeration system used for air conditioning or industrial cooling applications. They operate using screw compressors, which are efficient at handling large cooling loads.
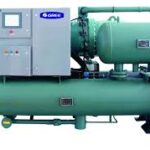
Oil Chiller
Oil Chiller are refrigeration systems designed to control and maintain the temperature of lubricating oil used in industrial machinery and processes. They ensure that the oil remains within a specified temperature range
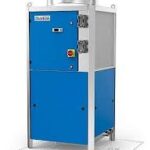
Hydraulic Oil Chiller
Hydraulic Oil Chillers are specialized refrigeration systems designed to cool and maintain the temperature of hydraulic oil used in hydraulic systems. They ensure that the oil remains within a specified temperature range
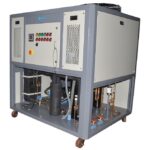
Online Chiller
Online Chiller is a refrigeration system designed to provide continuous cooling for industrial or commercial applications. It is equipped with capabilities for remote monitoring and control through internet connectivity
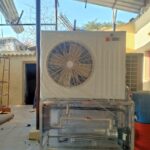
Glycol Chiller
Glycol Chiller is a type of cooling system that uses a glycol-water mixture as the coolant to remove heat from a process or equipment. Glycol chillers are commonly used
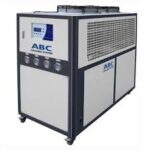
Spindle Chiller
Spindle Chiller are specialized cooling systems designed to manage the temperature of the spindle in machinery, such as CNC (Computer Numerical Control) machines.
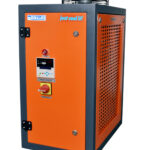
Refrigerated Air Dryer
Refrigerated Air Dryer is a type of device used in compressed air systems to reduce the moisture content of the air. It operates by cooling the compressed air to a temperature where water vapor condenses into liquid water.
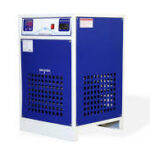