Spindle Chiller
Spindle Chiller are specialized cooling systems designed to manage the temperature of the spindle in machinery, such as CNC (Computer Numerical Control) machines. The spindle is a critical component that rotates at high speeds and can generate significant heat. Spindle chillers ensure that the spindle operates within an optimal temperature range to maintain precision, prolong equipment life, and prevent overheating and thermal damage. They typically use a closed-loop system with a refrigerant or coolant to dissipate heat efficiently.
Spindle Chiller
Characteristics of
- Precision Temperature Control: Spindle chillers maintain a consistent and precise temperature to ensure the spindle operates within the optimal range, which is critical for maintaining machining accuracy.
- High Cooling Capacity: They are designed to handle the substantial heat generated by high-speed spindles, providing effective cooling even under heavy loads.
- Compact Design: These chillers are typically compact to fit easily within the constrained spaces of CNC machine setups, ensuring they do not interfere with other components.
- Energy Efficiency: Many spindle chillers are designed to be energy-efficient, reducing operational costs and minimizing their environmental impact.
- Closed-Loop System: Spindle chillers often use a closed-loop cooling system, which recirculates the coolant to prevent contamination and maintain consistent cooling performance.
- Low Noise Operation: They are designed to operate quietly to maintain a conducive working environment in manufacturing facilities.
Spindle Chiller
Components of
- Coolant Reservoir: A tank to store the coolant, ensuring a steady supply for the cooling process.
- Pump: Circulates the coolant through the system, maintaining consistent flow and pressure.
- Heat Exchanger: Transfers heat from the spindle to the coolant efficiently. This can be an air-cooled or water-cooled heat exchanger.
- Filters: Remove impurities from the coolant to prevent contamination and ensure optimal cooling performance.
- Temperature Sensors: Monitor the temperature of the spindle and coolant, providing data for precise temperature control.
- Control Panel: A user interface for monitoring and adjusting the chiller’s settings, often featuring digital displays and programmable controls.
- Safety Alarms: Alert users to any operational issues, such as overheating, low coolant levels, or pump failures, ensuring timely intervention to prevent damage.
- Flow Meters: Measure the flow rate of the coolant to ensure it remains within the desired range for effective cooling.
- Bypass Valves: Allow for the diversion of coolant flow in case of system maintenance or failure, ensuring continued operation of the spindle.
- Expansion Tank: Accommodates the expansion and contraction of the coolant due to temperature changes, preventing pressure build-up in the system.
- Pressure Gauges: Monitor the pressure within the coolant circuit to ensure it remains within safe operating limits.
Spindle Chiller
Specification Details on
Model | Refrigeration Capacity | Chiller Water Flow | Heat Load | Equipment Type | Temperature Range | Coolant Type | Power Supply | Dimensions (L x W x H) | Weight | Noise Level | Control Type | Safety Features |
---|---|---|---|---|---|---|---|---|---|---|---|---|
SC-1000 | 1.5 kW | 10 L/min | 2 kW | Air-Cooled | 5°C – 35°C | Water/Glycol | 220V/50Hz | 600 x 400 x 800 mm | 50 kg | ≤ 60 dB | Digital | Overload Protection |
SC-2000 | 3 kW | 15 L/min | 4 kW | Air-Cooled | 5°C – 35°C | Water/Glycol | 220V/50Hz | 800 x 500 x 900 mm | 70 kg | ≤ 60 dB | Digital | Low Coolant Alarm |
SC-3000 | 5 kW | 20 L/min | 6 kW | Water-Cooled | 5°C – 35°C | Water/Glycol | 380V/50Hz | 1000 x 600 x 1000 mm | 100 kg | ≤ 60 dB | Digital | High Temp Alarm |
SC-4000 | 10 kW | 25 L/min | 12 kW | Water-Cooled | 5°C – 35°C | Water/Glycol | 380V/50Hz | 1200 x 700 x 1200 mm | 150 kg | ≤ 60 dB | Digital | Pressure Gauge |
SC-5000 | 15 kW | 30 L/min | 18 kW | Air-Cooled | 5°C – 35°C | Water/Glycol | 380V/50Hz | 1400 x 800 x 1400 mm | 200 kg | ≤ 65 dB | Digital | Flow Meter |
Other Chiller Products We Manufacture
Air Cooled Chiller
Air-cooled chillers are refrigeration systems that use air to dissipate heat from the coolant or refrigerant. Unlike water-cooled chiller, which rely on a water source and cooling towers
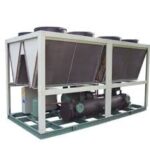
Water Cooled Chiller
Water Cooled Chillers are refrigeration systems that use water as a cooling medium to transfer heat away from the refrigerant. They are widely used in large-scale industrial
Screw Chiller
Screw Chillers are a type of refrigeration system used for air conditioning or industrial cooling applications. They operate using screw compressors, which are efficient at handling large cooling loads.
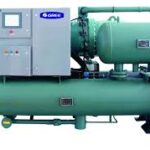
Variable Speed Chiller
Variable Speed Chillers are refrigeration systems equipped with compressors that have variable frequency drives (VFDs). These drives enable the compressor motor to adjust its speed according to the cooling load demand.
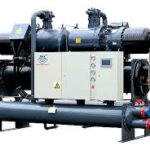
Oil Chiller
Oil Chiller are refrigeration systems designed to control and maintain the temperature of lubricating oil used in industrial machinery and processes. They ensure that the oil remains within a specified temperature range
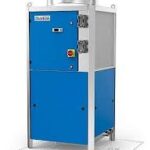
Hydraulic Oil Chiller
Hydraulic Oil Chillers are specialized refrigeration systems designed to cool and maintain the temperature of hydraulic oil used in hydraulic systems. They ensure that the oil remains within a specified temperature range
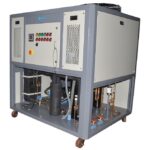
Online Chiller
Online Chiller is a refrigeration system designed to provide continuous cooling for industrial or commercial applications. It is equipped with capabilities for remote monitoring and control through internet connectivity
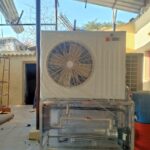
Glycol Chiller
Glycol Chiller is a type of cooling system that uses a glycol-water mixture as the coolant to remove heat from a process or equipment. Glycol chillers are commonly used in applications where maintaining a consistent
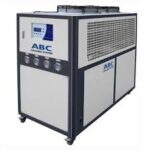
Refrigerated Air Dryer
Refrigerated Air Dryer is a type of device used in compressed air systems to reduce the moisture content of the air. It operates by cooling the compressed air to a temperature where water vapor condenses into liquid water.
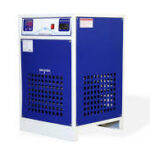