Shell and Tube Oil Cooler
Shell and Tube Oil Coolers are a type of heat exchanger commonly used in industrial applications to cool oil. These coolers consist of a series of tubes (tube bundle) enclosed within a cylindrical shell. The hot oil flows through the tubes, while a cooling fluid (usually water or air) circulates around the outside of the tubes within the shell. Heat is transferred from the oil to the cooling fluid, lowering the temperature of the oil. This design is efficient for high-pressure and high-temperature applications due to its robust construction and ability to handle large volumes of fluid.
Shell and Tube Oil Cooler
Specification of
Shell and Tube Oil Cooler
Operations of
- Flow Arrangement:
- Counterflow
- Parallel Flow
- Crossflow
- Heat Exchange Process:
- Oil flows through tubes.
- Cooling fluid circulates around tubes within the shell.
- Heat transfers from oil to cooling fluid through tube walls.
- Temperature Control:
- Thermostats and valves regulate flow rates.
- Bypass mechanisms manage temperature effectively.
Shell and Tube Oil Cooler
Characteristics of
- Durable Materials: Constructed from materials such as stainless steel, carbon steel, and copper alloys, which are known for their strength and longevity.
- Corrosion Resistance: These materials also provide excellent resistance to corrosion, ensuring the cooler can withstand harsh environments.
- Large Surface Area: The design includes a large surface area for heat exchange, facilitating efficient heat transfer from the oil to the cooling fluid.
- Effective Design: The arrangement of tubes and baffles maximizes the contact area between the fluids, enhancing heat exchange efficiency.
- High Pressure Capability: Designed to operate under high pressures, making them suitable for applications involving high-pressure fluids.
- Structural Integrity: The robust construction ensures the cooler can handle significant pressure without deformation or failure.
Other Heat Exchanger We Manufacture
Shell and Tube Condenser
Shell and Tube Condenser is a type of heat exchanger used to condense steam or vapor into liquid. It consists of a series of tubes enclosed within a cylindrical shell.
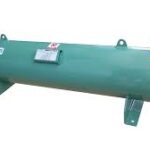
Shell and Tube Evaporator
Evaporator is a device used in refrigeration and air conditioning systems to absorb heat from its surroundings and evaporate a refrigerant. It operates by allowing the refrigerant
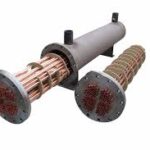
Shell and Tube After Coolers
Shell and Tube After Coolers are heat exchangers designed to cool compressed air or gases after they have been compressed by a compressor they consist of a bundle of tubes
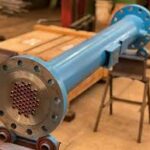
Shell and Tube Inter Coolers
Shell and Tube Inter Coolers is a type of heat exchanger commonly used in various industrial applications to cool fluids or gases. It consists of a series of tubes (tube bundle)
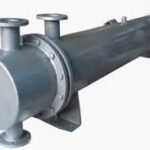
Removable Tube Heat Exchanger
Removable Tube Heat Exchanger is a heat exchanger designed with components that can be easily disassembled for maintenance, inspection, and cleaning.
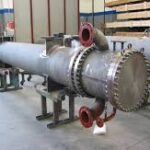
Fixed Tube Heat Exchangers
The Fixed Tube Sheet Heat Exchanger has a stationary tube sheet, securing heat exchange tubes for stability and integrity. It’s ideal for industrial applications
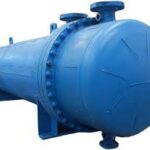
Tube Bundle Heat Exchanger
Tube Bundles are assemblies of multiple tubes, held together by tube sheets at either end. They are primarily used in shell and tube heat exchangers
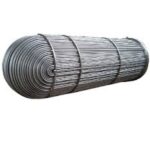
U-Tube Heat Exchanger
U-tube Heat Exchangers have U-shaped tubes that allow for thermal expansion and contraction, reducing stress. Efficient for high temperatures and pressures,
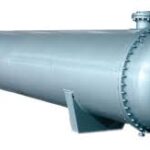