Shell and Tube After Coolers
Shell and Tube After Coolers are heat exchangers designed to cool compressed air or gases after they have been compressed by a compressor. They consist of a bundle of tubes through which the hot compressed air flows, surrounded by a shell through which a cooling fluid (often water or air) circulates. The heat from the compressed air transfers to the cooling fluid, reducing the temperature of the compressed air before it enters downstream equipment or processes.
Shell and Tube After Coolers
Specification of
DRAUGHT TYPE/ SHAPE | FLOW TYPE | MOC | CAPACITY (TR) | FILL TYPE | DRIVE TYPE |
---|---|---|---|---|---|
Forced / Rectangular | Counter Flow | Carbon Steel | 50 – 800 | Film Fills | Direct |
Induced / Round | Cross Flow | Titanium | 10 – 400 | Splash Fills | Belt Drive |
Forced / Square | Parallel Flow | Stainless Steel | 100 – 1200 | Honeycomb Fills | Gear Drive |
Induced / Oval | Counter Flow | Aluminum | 30 – 600 | Cellular Fills | Direct |
Forced / Triangular | Cross Flow | Copper | 15 – 300 | Splash Fills | Belt Drive |
Shell and Tube After Coolers
Advantages of
- Energy Efficiency: Reduces energy consumption by lowering the temperature of compressed air, improving overall system efficiency.
- Environmental Impact: Helps meet environmental regulations by reducing emissions associated with compressed air cooling.
- Longevity: Extends the lifespan of downstream equipment by delivering cooler and drier compressed air, reducing maintenance and replacement costs.
- Process Optimization: Optimizes process efficiency and quality by providing consistent and controlled temperatures for compressed air or gases.
- Compact Design: Offers a compact and space-efficient solution for cooling compressed air compared to other cooling methods, saving valuable floor space in industrial settings.
Shell and Tube After Coolers
Key Factors Involved
- Material of Construction (MOC): Determines compatibility with compressed air or gases and cooling fluids, as well as resistance to corrosion.
- Design Pressure and Temperature: Specifies the maximum operating conditions the aftercooler can withstand safely.
- Surface Area and Tube Layout: Influences heat transfer efficiency and pressure drop across the aftercooler.
- Flow Rates: Balances cooling efficiency with energy consumption based on the required throughput of compressed air or gases.
- Cooling Media: Determines the type (water, air) and availability of the cooling media to achieve desired cooling effects.
- Maintenance Requirements: Regular cleaning and inspection to prevent fouling and ensure optimal performance.
Other Heat Exchanger We Manufacture
Shell and Tube Condenser
Shell and Tube Condenser is a type of heat exchanger used to condense steam or vapor into liquid. It consists of a series of tubes enclosed within a cylindrical shell.
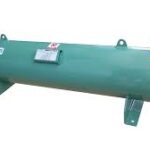
Shell and Tube Evaporator
Evaporator is a device used in refrigeration and air conditioning systems to absorb heat from its surroundings and evaporate a refrigerant. It operates by allowing the refrigerant
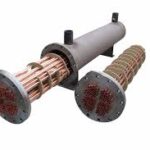
Shell and Tube Inter Coolers
Shell and Tube Inter Coolers is a type of heat exchanger commonly used in various industrial applications to cool fluids or gases. It consists of a series of tubes (tube bundle)
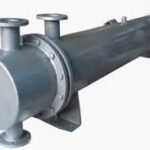
Shell and Tube Oil Coolers
Shell and Tube Oil Coolers are a type of heat exchanger commonly used in industrial applications to cool oil. These coolers consist of a series of tubes (tube bundle)
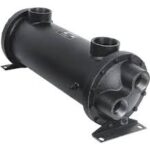
Removable Tube Heat Exchanger
Removable Tube Heat Exchanger is a heat exchanger designed with components that can be easily disassembled for maintenance, inspection, and cleaning.
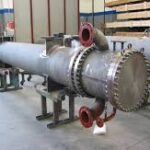
Fixed Tube Heat Exchangers
The Fixed Tube Sheet Heat Exchanger has a stationary tube sheet, securing heat exchange tubes for stability and integrity. It’s ideal for industrial applications
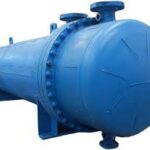
Tube Bundle Heat Exchanger
Tube Bundles are assemblies of multiple tubes, held together by tube sheets at either end. They are primarily used in shell and tube heat exchangers
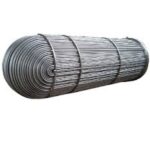
U-Tube Heat Exchanger
U-tube Heat Exchangers have U-shaped tubes that allow for thermal expansion and contraction, reducing stress. Efficient for high temperatures and pressures,
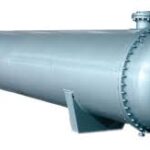