Removable Tube Heat Exchangers
Removable Tube Heat Exchanger is a heat exchanger designed with components that can be easily disassembled for maintenance, inspection, and cleaning. This typically includes features like removable tube bundles or tube sheets, allowing access to both the shell and tube sides without dismantling the entire unit. This design enhances maintainability and prolongs the equipment’s lifespan, making it suitable for applications where regular maintenance is required.
Removable Tube Heat Exchangers
Key Factors involved
- Material of Construction:
The materials used for the tubes, shell, and other components must resist corrosion and withstand high temperatures and pressures. Common materials include stainless steel, carbon steel, copper, and titanium.
- Tube Bundle Design:
The removable tube bundle allows for easy maintenance and cleaning, which is essential for preventing fouling and scaling that can reduce efficiency.
- Heat Transfer Efficiency:
The surface area of the tubes, the thermal conductivity of the materials, and the flow arrangement (e.g., counterflow, parallel flow) significantly impact the efficiency of heat transfer.
- Flow Arrangement:
The number of passes and the flow type (single-pass, multi-pass) affect the heat exchanger’s performance and the pressure drop across the system.
- Baffle Design:
The type and spacing of baffles (e.g., segmental, helical) enhance the turbulence of the shell-side fluid, improving heat transfer but also impacting pressure drop.
- Maintenance Accessibility:
Easy access to the tube bundle for inspection, cleaning, and replacement is crucial for maintaining performance and prolonging the heat exchanger’s lifespan.
- Design Pressure and Temperature:
The maximum operating pressure and temperature ratings must match the application’s requirements to ensure safety and reliability.
- Size and Dimensions:
The physical size and configuration of the heat exchanger must fit within the available space and meet the process requirements.
Removable Tube Heat Exchangers
Advantages of
- Ease of Maintenance:
The removable tube bundle allows for easy access to both the shell and tube sides, facilitating cleaning, inspection, and repairs. This helps maintain optimal heat transfer efficiency and extends the equipment’s lifespan.
- Flexibility:
The design can accommodate different materials and configurations to suit various process requirements, making it adaptable for a wide range of applications.
- Efficient Cleaning:
The ability to remove the tube bundle simplifies the process of cleaning and descaling, which is essential for preventing fouling and maintaining efficient operation.
- Reduced Downtime:
Easy maintenance and quick tube bundle removal reduce downtime during routine inspections and repairs, improving overall system availability and productivity.
- Enhanced Durability:
The construction materials and design can be tailored to resist corrosion, high temperatures, and pressures, ensuring long-term reliability and durability in harsh operating conditions.
- Improved Performance:
Regular maintenance facilitated by the removable design helps maintain peak heat transfer efficiency, leading to better performance and energy savings over time.
- Cost-Effective:
Although the initial investment may be higher, the long-term savings on maintenance, reduced downtime, and prolonged equipment life make removable tube heat exchangers a cost-effective solution.
Removable Tube Heat Exchangers
Technical Specification for
Feature | Description | Typical Values |
---|---|---|
Type | Heat Exchanger Type | Removable Tube Heat Exchanger |
Material | Material of Construction | Stainless Steel, Carbon Steel, Copper, Titanium |
Tube Diameter | Diameter of Tubes | 10mm – 30mm |
Tube Length | Length of Tubes | 1m – 6m |
Heat Transfer Area | Total Surface Area | 10 – 500 m² |
Shell Diameter | Diameter of Shell | 0.5m – 2m |
Design Pressure | Maximum Operating Pressure | 10 – 100 bar |
Design Temperature | Maximum Operating Temperature | -50°C to +400°C |
Flow Arrangement | Number of Passes | Single-pass, Two-pass, Multi-pass |
Baffles | Baffle Type and Spacing | Segmental, Helical; 100mm – 300mm spacing |
Connections | Inlet/Outlet Nozzles | 2″ – 12″ diameter, ANSI/DIN flanges |
Mounting | Support Structure | Saddle Supports, Bracket Mounts |
Standards and Codes | Compliance | ASME, TEMA, API, ISO |
Maintenance Access | Accessibility | Removable Tube Bundle, Easy Clean Access |
Weight | Weight of the Heat Exchanger | 200 – 5000 kg |
Other Heat Exchanger We Manufacture
Shell and Tube Condenser
Shell and Tube Condenser is a type of heat exchanger used to condense steam or vapor into liquid. It consists of a series of tubes enclosed within a cylindrical shell.
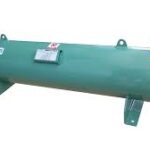
Shell and Tube Evaporator
Evaporator is a device used in refrigeration and air conditioning systems to absorb heat from its surroundings and evaporate a refrigerant. It operates by allowing the refrigerant
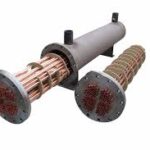
Shell and Tube After Coolers
Shell and Tube After Coolers are heat exchangers designed to cool compressed air or gases after they have been compressed by a compressor they consist of a bundle of tubes
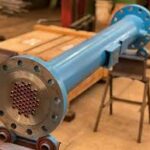
Shell and Tube Inter Coolers
Shell and Tube Inter Coolers is a type of heat exchanger commonly used in various industrial applications to cool fluids or gases. It consists of a series of tubes (tube bundle)
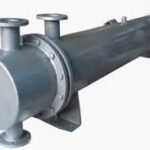
Shell and Tube Oil Coolers
Shell and Tube Oil Coolers are a type of heat exchanger commonly used in industrial applications to cool oil. These coolers consist of a series of tubes (tube bundle)
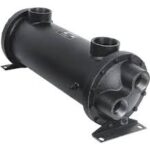
Fixed Tube Heat Exchangers
The Fixed Tube Sheet Heat Exchanger has a stationary tube sheet, securing heat exchange tubes for stability and integrity. It’s ideal for industrial applications
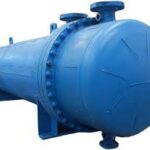
Tube Bundle Heat Exchanger
Tube Bundles are assemblies of multiple tubes, held together by tube sheets at either end. They are primarily used in shell and tube heat exchangers
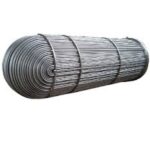
U-Tube Heat Exchanger
U-tube Heat Exchangers have U-shaped tubes that allow for thermal expansion and contraction, reducing stress. Efficient for high temperatures and pressures,
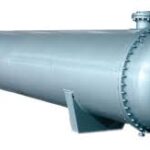