Glycol Chiller
Glycol Chiller is a type of cooling system that uses a glycol-water mixture as the coolant to remove heat from a process or equipment. Glycol chillers are commonly used in applications where maintaining a consistent and low temperature is crucial, such as in breweries, wineries, food processing, and HVAC systems. The glycol mixture prevents freezing and enhances the heat transfer properties of the coolant, making glycol chillers efficient and reliable for temperature-sensitive operations. These chillers typically feature components like compressors, heat exchangers, and pumps to circulate the glycol mixture and maintain the desired temperature.
Glycol Chiller
Advantages of
- Prevention of Freezing: Glycol, when mixed with water, lowers the freezing point of the coolant, which is particularly useful in low-temperature applications where water alone might freeze.
- Corrosion Inhibition: Glycol mixtures often contain additives that prevent corrosion, protecting the chiller system’s components and extending their lifespan.
- Efficient Heat Transfer: Glycol solutions can improve heat transfer efficiency, ensuring rapid and consistent cooling.
- Versatility: Glycol chillers can be used in various industries, including food and beverage, pharmaceuticals, HVAC, and industrial processes, making them highly versatile.
- Temperature Control: These chillers provide precise temperature control, which is crucial for processes requiring strict temperature maintenance.
Glycol Chiller
Types of
- Air-Cooled Glycol Chiller: Uses ambient air for heat dissipation, suitable for locations without water access.
- Water-Cooled Glycol Chiller: Utilizes water from a cooling tower or supply for efficient heat removal, ideal for high ambient temperature environments.
- Portable Glycol Chiller: Compact and movable units for flexible cooling solutions in temporary or event-based applications.
- Split System Glycol Chiller: Separates evaporator and condenser units for versatile installation options and reduced indoor noise.
- Packaged Glycol Chiller: Complete systems housed in a single unit for simplified installation and maintenance.
- Modular Glycol Chiller: Consists of multiple units that can be combined to scale capacity and enhance system reliability.
Glycol Chiller
Specification Details
Model | Refrigeration Capacity | Chiller Water Flow | Heat Load | Equipment Type | Temperature Range | Coolant Type | Power Supply | Dimensions (L x W x H) | Weight | Noise Level | Control Type | Safety Features |
---|---|---|---|---|---|---|---|---|---|---|---|---|
GC-1000 | 5 kW | 20 L/min | 6 kW | Air-Cooled | -10°C to 35°C | Water/Glycol | 220V/50Hz | 1200 x 600 x 1000 mm | 120 kg | ≤ 65 dB | Digital | Overload Protection |
GC-2000 | 10 kW | 40 L/min | 12 kW | Air-Cooled | -10°C to 35°C | Water/Glycol | 380V/50Hz | 1400 x 700 x 1100 mm | 180 kg | ≤ 65 dB | Digital | Low Coolant Alarm |
GC-3000 | 15 kW | 60 L/min | 18 kW | Water-Cooled | -10°C to 35°C | Water/Glycol | 380V/50Hz | 1600 x 800 x 1200 mm | 240 kg | ≤ 65 dB | Digital | High Temp Alarm |
GC-4000 | 20 kW | 80 L/min | 24 kW | Water-Cooled | -10°C to 35°C | Water/Glycol | 380V/50Hz | 1800 x 900 x 1300 mm | 300 kg | ≤ 65 dB | Digital | Pressure Gauge |
GC-5000 | 25 kW | 100 L/min | 30 kW | Air-Cooled | -10°C to 35°C | Water/Glycol | 380V/50Hz | 2000 x 1000 x 1400 mm | 360 kg | ≤ 70 dB | Digital | Flow Meter, Overload Alarm |
Other Chiller Products We Manufacture
Air Cooled Chiller
Air-cooled chillers are refrigeration systems that use air to dissipate heat from the coolant or refrigerant. Unlike water-cooled chiller, which rely on a water source and cooling towers
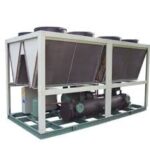
Water Cooled Chiller
Water Cooled Chillers are refrigeration systems that use water as a cooling medium to transfer heat away from the refrigerant. They are widely used in large-scale industrial
Screw Chiller
Screw Chillers are a type of refrigeration system used for air conditioning or industrial cooling applications. They operate using screw compressors, which are efficient at handling large cooling loads.
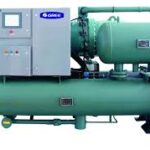
Variable Speed Chiller
Variable Speed Chillers are refrigeration systems equipped with compressors that have variable frequency drives (VFDs). These drives enable the compressor motor to adjust its speed according to the cooling load demand.
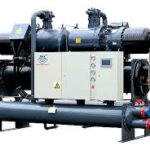
Oil Chiller
Oil Chiller are refrigeration systems designed to control and maintain the temperature of lubricating oil used in industrial machinery and processes. They ensure that the oil remains within a specified temperature range
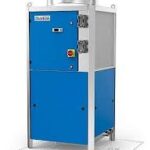
Hydraulic Oil Chiller
Hydraulic Oil Chillers are specialized refrigeration systems designed to cool and maintain the temperature of hydraulic oil used in hydraulic systems. They ensure that the oil remains within a specified temperature range
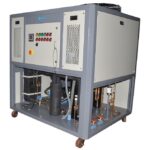
Online Chiller
Online Chiller is a refrigeration system designed to provide continuous cooling for industrial or commercial applications. It is equipped with capabilities for remote monitoring
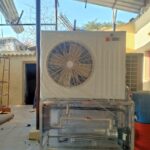
Spindle Chiller
Spindle Chiller are specialized cooling systems designed to manage the temperature of the spindle in machinery, such as CNC (Computer Numerical Control) machines.
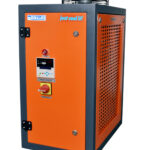
Refrigerated Air Dryer
Refrigerated Air Dryer is a type of device used in compressed air systems to reduce the moisture content of the air. It operates by cooling the compressed air to a temperature where water vapor condenses into liquid water.
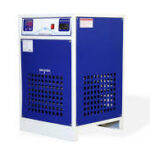