Gasketed Plate Heat Exchanger
Gasketed Plate Heat Exchangers use thin, corrugated plates in a frame, sealed with gaskets, to efficiently transfer heat between fluids. The corrugations increase surface area and turbulence, enhancing heat exchange. Compact, efficient, and easy to maintain, GPHEs are used in HVAC, food and beverage processing, chemical processing, and power generation due to their versatility.
Gasketed Plate Heat Exchanger
Key Factors in
Gasketed Plate Heat Exchanger
Applications of
- Heat Recovery Systems: Used in industrial processes, HVAC systems, and power generation plants to recover heat from exhaust gases, process streams, or wastewater for reuse in heating or preheating applications.
- HVAC Systems: Found in commercial and residential buildings for heating and cooling applications, including air conditioning units, heat pumps, and district heating and cooling systems.
- Refrigeration Systems: Used in refrigeration units and chillers for heat exchange between refrigerants and process fluids, such as in supermarkets, cold storage facilities, and food processing plants.
- Chemical Processing: Utilized in chemical reactors, refineries, and petrochemical plants for heating and cooling process fluids, including corrosive or aggressive substances.
- Power Generation: Found in thermal power plants, cogeneration systems, and renewable energy facilities for heat exchange in steam turbines, boilers, and waste heat recovery units.
- Marine and Offshore Applications: Used on ships and offshore platforms for seawater cooling systems, HVAC systems, and various heat transfer duties in harsh environmental conditions.
- Water Treatment: Found in water desalination plants, wastewater treatment facilities, and industrial water recycling systems for heat exchange in water purification processes.
- Renewable Energy: Utilized in solar thermal systems for heating water or heat transfer fluids using solar energy, contributing to renewable energy generation and sustainability efforts.
Gasketed Plate Heat Exchanger
Types of
- Standard Gasketed Plate Heat Exchangers: The plates are typically corrugated to create turbulence and enhance heat transfer efficiency.
- Brazed Plate Heat Exchangers (BPHE): BPHEs are compact and offer efficient heat transfer, suitable for HVAC, refrigeration, and industrial applications.
- Welded Plate Heat Exchangers: This type is less common than brazed plate exchangers due to higher costs and limitations in disassembly for maintenance.
- Semi-Welded Plate Heat Exchangers: They are used in industries requiring heat exchange between fluids with different levels of contamination or where gasketed plates alone may not withstand the operating conditions.
Other Plate Heat Exchanger We Manufacture
Brazed Plate Heat Exchanger
Brazed Plate Heat Exchanger (BPHE) is a type of heat exchanger that incorporates several corrugated plates with a brazing material between each plate.
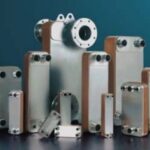
Shell and Tube Condenser
Shell and Tube Condenser is a type of heat exchanger used to condense steam or vapor into liquid. It consists of a series of tubes enclosed within a cylindrical shell.
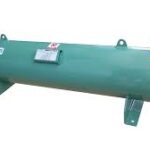
Shell and Tube Evaporator
Evaporator is a device used in refrigeration and air conditioning systems to absorb heat from its surroundings and evaporate a refrigerant. It operates by allowing the refrigerant
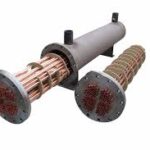
Shell and Tube After Coolers
Shell and Tube After Coolers are heat exchangers designed to cool compressed air or gases after they have been compressed by a compressor they consist of a bundle of tubes
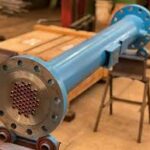
Shell and Tube Inter Coolers
Shell and Tube Inter Coolers is a type of heat exchanger commonly used in various industrial applications to cool fluids or gases. It consists of a series of tubes (tube bundle)
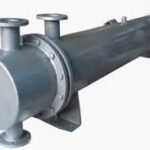
Shell and Tube Oil Coolers
Shell and Tube Oil Coolers are a type of heat exchanger commonly used in industrial applications to cool oil. These coolers consist of a series of tubes (tube bundle)
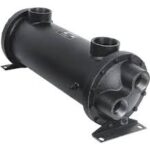