Foundry Sand Cooler
Foundry Sand Cooler is a piece of equipment used in foundries to cool hot sand after it has been used in the casting process. The cooling process is essential to prepare the sand for reuse in subsequent casting cycles. These coolers often use water or air as the cooling medium and may include additional features like moisture control and sand conditioning to ensure the sand retains its desired properties. This helps maintain the quality of the sand and improves the efficiency and effectiveness of the foundry operations.
Foundry Sand Cooler
Features of
- Efficient Cooling Mechanism: Utilizes air, water, or a combination of both to rapidly reduce the temperature of the sand.
- Moisture Control: Integrated systems to add or remove moisture, ensuring the sand has the optimal moisture content for reuse.
- Even Sand Distribution: Mechanisms to evenly distribute the sand within the cooler, promoting uniform cooling.
- Temperature Monitoring: Sensors and controls to continuously monitor and regulate the temperature of the sand.
- High Throughput: Designed to handle large volumes of sand, matching the high production rates of modern foundries.
- Durable Construction: Made from robust materials to withstand the abrasive nature of sand and the harsh foundry environment.
- Compact Design: Space-efficient designs to fit into limited spaces within the foundry layout.
- Easy Maintenance: Features for easy access and maintenance to minimize downtime.
Foundry Sand Cooler
Specification on
- Cooling Capacity: The amount of sand the cooler can process per hour, typically measured in tons per hour (TPH).
- Cooling Medium: Specifies whether the cooler uses air, water, or a combination of both as the cooling medium.
- Temperature Reduction: The expected drop in sand temperature, often detailed as the range from the initial sand temperature to the final cooled temperature.
- Moisture Control Range: The capability to adjust the sand’s moisture content, typically specified as a percentage range.
- Power Consumption: The amount of electrical power required to operate the cooler, usually measured in kilowatts (kW).
- Water Consumption: For water-cooled systems, the volume of water used, measured in gallons per minute (GPM) or liters per minute (LPM).
Foundry Sand Cooler
Design Features of
- Sand Distribution and Feed System: Designed to ensure even distribution and continuous feed of sand into the cooler, often using vibratory feeders or screw conveyors.
- Moisture Control Mechanism: Integrated systems, such as water spray bars or steam injectors, to adjust the moisture content of the sand, ensuring it meets the desired specifications for reuse.
- Agitation and Mixing: Mechanisms like paddles, augers, or rotary drums to continuously agitate and mix the sand, ensuring uniform cooling and consistent moisture distribution.
Foundry Sand Cooler
Capacity Range of
Type of Sand Cooler | Capacity (TPH) | Application |
---|---|---|
Small-Scale Foundry Sand Coolers | ||
Batch Coolers | 1 to 5 | Smaller foundry operations, specialized applications |
Portable Coolers | 0.5 to 2 | Small batches, mobile operations |
Medium-Scale Foundry Sand Coolers | ||
Rotary Drum Coolers | 5 to 20 | Mid-sized foundries |
Fluidized Bed Coolers | 10 to 30 | Medium capacities, efficient cooling |
Large-Scale Foundry Sand Coolers | ||
Continuous Flow Coolers | 20 to 100 | Large foundries with high production rates |
High-Capacity Rotary Drum Coolers | 30 to 100 | Large volumes |
Specialized High-Capacity Coolers | ||
Customized Industrial Coolers | Over 100 | Very large foundries, specific industrial applications |
Other Finned Tube Heat Exchanger We Manufacture
Chilled Water Finned Tube Coils
Chilled Water Finned Tube Coils are components used in HVAC systems for cooling. They consist of a series of tubes with external fins that increase surface area for heat transfer.
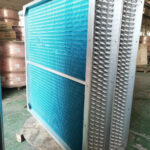
Air Handling Unit
Air Handling Unit (AHU) coil is a vital component in HVAC systems, designed to heat or cool air. It comprises tubes through which refrigerant or water circulates and fins that increase
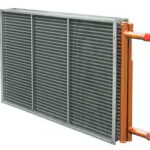
Fin Tube Evaporator Coil
Fin Tube Evaporator coil is a heat exchanger used in air conditioning and refrigeration systems. It consists of copper or aluminum tubes with aluminum fins attached to them.
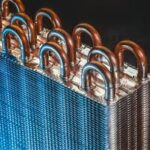
Fan Coil Unit
Fan Coil Unit (FCU) is a device used in HVAC systems to control the temperature and airflow in a space. It typically consists of a heat exchanger (coil) connected to a fan
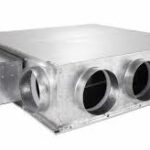
Hot Water Steam Coils
Hot Water Steam Coils are heat exchangers used in HVAC systems to transfer heat from hot water or steam to air. They consist of tubes, usually made of copper or steel,
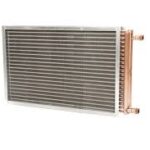
Air Cooled Heat Exchanger
Air Cooled Heat Exchangers (ACHEs) are devices that transfer heat from a fluid (liquid or gas) to the surrounding air. They use finned tubes to increase the surface area for heat transfer
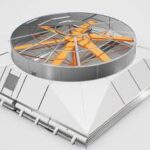
Rice Mill Heat Exchanger
Rice Mill Heat Exchanger is a device used to regulate and control the temperature during various stages of rice milling, such as drying, parboiling, and cooling.
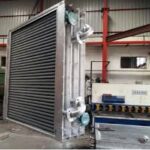
Air Blast Oil Cooler
Air Blast Oil Cooler is a heat exchanger used to cool hydraulic oil, lubricating oil, or other fluids in industrial machinery and automotive applications.
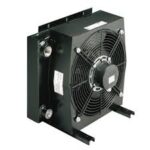
Aluminum Finned Water Tube Coils
Aluminum Finned Water Tube Coils are heat exchangers used in HVAC systems to transfer heat between air and water. They consist of tubes, typically made of copper or another material
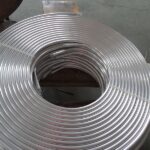