Fixed Tube Sheet Heat Exchangers
The Fixed Tube Sheet Heat Exchanger has a stationary tube sheet, securing heat exchange tubes for stability and integrity. It’s ideal for industrial applications, accommodating thermal expansion while simplifying maintenance and ensuring efficient heat transfer. Suitable for chemical plants, refineries, and HVAC systems, it offers reliability and durability.
Fixed Tube Sheet Heat Exchangers
Operations
- Fluid Flow:
- Tube Side: One fluid (the tube-side fluid) flows through the tubes.
- Shell Side: Another fluid (the shell-side fluid) flows over the outside of the tubes within the shell.
- Heat Transfer:
- The hot fluid (either on the tube side or shell side) transfers heat to the cooler fluid.
- This process involves conduction through the tube walls and convection on both the inside and outside of the tubes.
- Thermal Expansion:
- Because the tube sheets are fixed, the design must accommodate the differential thermal expansion of the tubes and shell. This is often managed by using expansion joints or flexible tube materials.
- Heat Exchange Process:
- Counterflow: Fluids flow in opposite directions, maximizing the temperature gradient and improving heat transfer efficiency.
- Parallel Flow: Fluids flow in the same direction, resulting in lower heat transfer efficiency but simplified construction.
Fixed Tube Sheet Heat Exchangers
Types of
- Simple Tube Sheet Heat Exchanger: This basic type features straight tubes fixed at both ends to a single tube sheet, typically used in simpler industrial applications.
- U-Tube Heat Exchanger: In this design, the tubes are bent into a U-shape with both ends fixed to a single tube sheet, allowing for thermal expansion without stressing the tubes.
- Double Tube Sheet Heat Exchanger: Utilizes two tube sheets with the tube bundle held between them, reducing the risk of fluid cross-contamination in critical applications like chemical processing.
- Kettle Type Reboiler: In this specialized design, a shell encloses a tube bundle with both ends fixed to separate tube sheets, used primarily in distillation and process heating.
- Bayonet Type Heat Exchanger: Features a tube bundle with one end fixed to a tube sheet inside a shell, while the other end extends through the shell for direct heating or cooling of another fluid.
Fixed Tube Sheet Heat Exchangers
Benefits of
- Reliability: The stationary tube sheet design ensures that tubes remain securely fixed in place, reducing the risk of tube damage or failure during operation.
- Cost-Effectiveness: They generally have lower initial costs and reduced maintenance requirements compared to other heat exchanger designs.
- Suitability for High Pressure and Temperature: Fixed tube sheet exchangers are well-suited for applications involving high pressures and temperatures, as the stationary design enhances structural integrity.
- Simplicity: Their straightforward construction makes them easier to operate and maintain, with fewer components susceptible to wear or malfunction.
- Versatility: Available in various materials and configurations, they can be tailored to meet specific process requirements across different industries.
- Efficient Heat Transfer: The fixed arrangement minimizes thermal stresses and allows for efficient heat exchange between fluids.
Other Heat Exchanger We Manufacture
Shell and Tube Condenser
Shell and Tube Condenser is a type of heat exchanger used to condense steam or vapor into liquid. It consists of a series of tubes enclosed within a cylindrical shell.
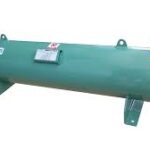
Shell and Tube Evaporator
Evaporator is a device used in refrigeration and air conditioning systems to absorb heat from its surroundings and evaporate a refrigerant. It operates by allowing the refrigerant
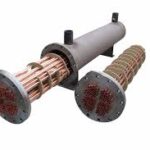
Shell and Tube After Coolers
Shell and Tube After Coolers are heat exchangers designed to cool compressed air or gases after they have been compressed by a compressor they consist of a bundle of tubes
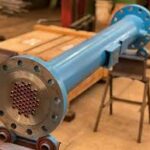
Shell and Tube Inter Coolers
Shell and Tube Inter Coolers is a type of heat exchanger commonly used in various industrial applications to cool fluids or gases. It consists of a series of tubes (tube bundle)
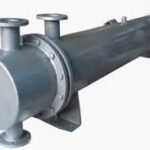
Shell and Tube Oil Coolers
Shell and Tube Oil Coolers are a type of heat exchanger commonly used in industrial applications to cool oil. These coolers consist of a series of tubes (tube bundle)
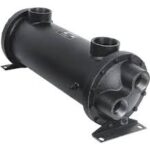
Removable Tube Heat Exchanger
Removable Tube Heat Exchanger is a heat exchanger designed with components that can be easily disassembled for maintenance, inspection, and cleaning.
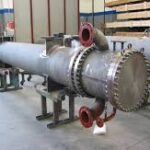
Tube Bundle Heat Exchanger
Tube Bundles are assemblies of multiple tubes, held together by tube sheets at either end. They are primarily used in shell and tube heat exchangers
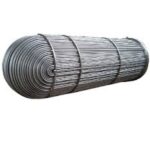
U-Tube Heat Exchanger
U-tube Heat Exchangers have U-shaped tubes that allow for thermal expansion and contraction, reducing stress. Efficient for high temperatures and pressures,
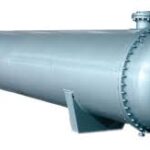