Copper Pipes and Fittings
Copper Pipes and Fittings are commonly used in plumbing and HVAC systems due to their durability, corrosion resistance, and excellent heat transfer properties. Pipes made of copper are known for their reliability in carrying water and gases, while fittings such as elbows, tees, and couplings allow for flexible configurations and connections. Copper’s versatility and longevity make it a preferred material in residential, commercial, and industrial applications where durability and efficient fluid transfer are essential.
Copper Pipes and Fittings
Material and Components of
Component/Material | Description |
---|---|
Copper Pipes | Durable and corrosion-resistant, used for conveying water, gases, and fluids in plumbing and HVAC systems. |
Elbows | Fittings used to change the direction of piping at an angle, typically 90 degrees or 45 degrees. |
Tees | Fittings with three openings used to join three pipes or create branch lines in plumbing systems. |
Couplings | Connectors used to join two pipes together, often used for repairs or extensions in plumbing. |
Adapters | Fittings that facilitate connections between pipes of different materials or sizes. |
Reducers | Fittings that transition between pipes of different diameters, reducing flow rate or pressure. |
Caps and Plugs | Fittings used to seal the end of a pipe, preventing leakage and providing access for maintenance. |
Flanges | Used to connect pipes, valves, or equipment in a piping system, providing ease of assembly and disassembly. |
Valves | Control devices used to regulate flow, pressure, and direction of fluids within a piping system. |
Strainers and Filters | Devices used to remove debris and particles from fluids flowing through the piping system. |
Insulation | Material used to wrap around pipes to prevent heat loss or gain and protect against freezing. |
Copper Pipes and Fittings
Essential and Components
- Conveying Refrigerant: Copper pipes are used to transport refrigerant between the chiller components, such as the compressor, condenser, expansion valve, and evaporator. They ensure the efficient flow of refrigerant, which is essential for the chiller’s cooling process.
- Heat Transfer: Copper’s excellent thermal conductivity facilitates efficient heat transfer within the chiller system. This property allows for effective heat exchange between the refrigerant and the surroundings, optimizing cooling performance.
- Corrosion Resistance: Copper pipes and fittings are highly resistant to corrosion, ensuring long-term durability and maintaining the integrity of the chiller system. This resistance is crucial given the presence of moisture and chemicals in refrigeration applications.
- Flexibility and Versatility: Copper fittings, such as elbows, tees, and couplings, provide flexibility in configuring the chiller system layout. They allow for precise routing of piping to accommodate space constraints and optimize flow dynamics.
Other Chiller Spares We Manufacture
Scroll Compressor
A scroll compressor is a type of positive displacement compressor that uses two interleaved spiral-shaped scrolls to compress gas. One scroll is stationary,

Semi-hermetic Compressor
A semi-hermetic compressor is a type of compressor where the motor and compressor are enclosed in a single, sealed housing, but unlike fully hermetic compressors,
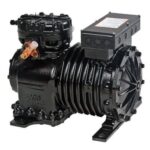
Hermetic Compressor
Hermetic Compressor is a type of compressor widely used in refrigeration and air conditioning systems. It features an airtight housing that encloses both the motor and the compressor,
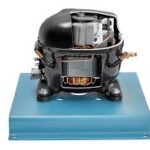
Screw Compressor
Screw Compressor is a type of rotary compressor that uses two intermeshing helical rotors to compress gas or air. As the rotors rotate, they trap and compress the gas
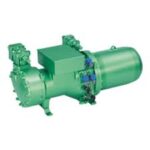
Reciprocating Compressor
A reciprocating compressor is a positive displacement device that compresses gas by using a piston driven by a crankshaft. The piston moves back and forth in a cylinder
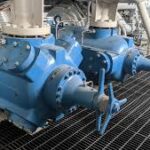
Rotary Compressor
Rotary Compressor is a type of gas compressor that uses a rotating mechanism, such as screws, vanes, or scrolls, to compress gas. The rotating elements trap and compress
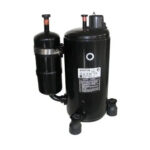
Refrigeration Gases
Refrigeration Gases, also known as refrigerants, are substances used in refrigeration systems to transfer heat from one area to another through a cycle of evaporation and condensation.
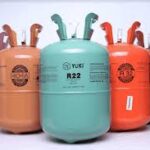
Axil Fan
Axil Fan is a type of mechanical fan commonly used for moving air or gas parallel to the axis of its blades. Unlike centrifugal fans that generate airflow perpendicular to the fan blades
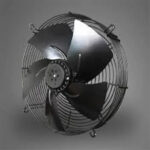
Condenser
Condenser is a key component in refrigeration and air conditioning systems that facilitates the transfer of heat absorbed by the refrigerant to the outside environment.
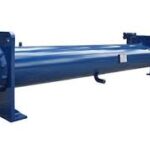
Chiller Pumps
Chiller Pumps, also known as condenser water pumps or circulation pumps, are essential components in chiller systems. Their primary function is to circulate water
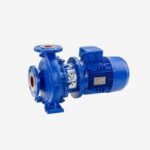
Chiller Control Panel
Chiller Control Panel is a centralized component of a chiller system that oversees and regulates the operation of key components such as compressors, pumps
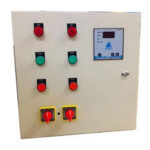
Expansion Valves
Expansion Valves are mechanical devices used in refrigeration and air conditioning systems to regulate the flow of refrigerant into the evaporator. They maintain a controlled reduction
