Air Cooled Chiller
Air-cooled chillers are refrigeration systems that use air to dissipate heat from the coolant or refrigerant. Unlike water-cooled chiller, which rely on a water source and cooling towers, air-cooled chiller use fans to blow air over condenser coils, transferring heat from the refrigerant to the ambient air. They are typically used in smaller to medium-sized applications, such as commercial buildings and industrial processes, where water availability or cost is a concern. These chillers are valued for their relatively simple installation, lower maintenance requirements, and suitability for environments where water conservation is important.
Air Cooled Chiller
Characteristics of
- Cooling Mechanism: Air-cooled chillers use air to remove heat from the refrigerant. The refrigerant absorbs heat from the chilled water in the evaporator, then travels to the condenser where fans blow air over the coils, releasing the absorbed heat into the atmosphere.
- Heat Exchanger: The condenser coils facilitate the heat transfer from the refrigerant to the surrounding air. As the refrigerant releases heat, it changes from a high-pressure vapor to a high-pressure liquid.
- Refrigerant: A fluid, usually a hydrofluorocarbon (HFC), that circulates within the chiller, absorbing heat at the evaporator and releasing it at the condenser. Common refrigerants include R-410A and R-134a.
Air Cooled Chiller
Energy Efficiency on
- SEER (Seasonal Energy Efficiency Ratio): A measure of cooling efficiency over a typical cooling season, taking into account variations in load and ambient temperature.
- EER (Energy Efficiency Ratio): A measure of the cooling efficiency at a specific operating condition, typically used to compare the efficiency of different chillers under standard conditions.
- Variable Speed Drives: Improve energy efficiency by adjusting the speed of the compressor and fans based on the cooling load, reducing energy consumption during partial load conditions.
Air Cooled Chiller
Components of
- Compressor: The compressor is the heart of the air-cooled chiller. It compresses the refrigerant, significantly raising its pressure and temperature. This high-pressure, high-temperature refrigerant gas is then sent to the condenser.
- Condenser Coils: Heat exchangers where the high-pressure refrigerant releases its heat to the air blown over the coils by the fans.
- Evaporator: Another heat exchanger where the refrigerant absorbs heat from the chilled water or other fluid, thus cooling it down.
- Expansion Valve: Regulates the flow of refrigerant into the evaporator, lowering its pressure and temperature to enhance heat absorption.
- Fans: Blow air over the condenser coils to assist in the heat dissipation process. Can be axial or centrifugal, depending on the design requirements.
- Control System: Manages the operation of the chiller, including starting/stopping the compressor, adjusting fan speeds, and optimizing overall performance for energy efficiency.
- Piping and Valves: Connect the various components and control the flow of refrigerant and chilled fluid through the system.
- Electrical Components: Include wiring, switches, circuit boards, and other elements that power and control the chiller’s operation.
Other Chiller Products We Manufacture
Water Cooled Chiller
Water Cooled Chillers are refrigeration systems that use water as a cooling medium to transfer heat away from the refrigerant. They are widely used in large-scale industrial
Screw Chiller
Screw Chillers are a type of refrigeration system used for air conditioning or industrial cooling applications. They operate using screw compressors
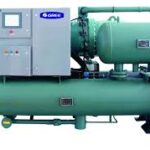
Variable Speed Chiller
Variable Speed Chillers are refrigeration systems equipped with compressors that have variable frequency drives (VFDs). These drives enable the compressor motor to adjust its speed according to the cooling load demand.
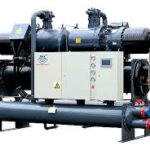
Oil Chiller
Oil Chiller are refrigeration systems designed to control and maintain the temperature of lubricating oil used in industrial machinery and processes. They ensure that the oil remains within a specified temperature range
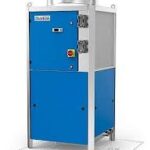
Hydraulic Oil Chiller
Hydraulic Oil Chillers are specialized refrigeration systems designed to cool and maintain the temperature of hydraulic oil used in hydraulic systems. They ensure that the oil remains within a specified temperature range
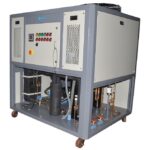
Online Chiller
Online Chiller is a refrigeration system designed to provide continuous cooling for industrial or commercial applications. It is equipped with capabilities for remote monitoring and control through internet connectivity
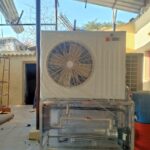
Glycol Chiller
Glycol Chiller is a type of cooling system that uses a glycol-water mixture as the coolant to remove heat from a process or equipment Glycol chillers
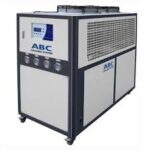
Spindle Chiller
Spindle Chiller are specialized cooling systems designed to manage the temperature of the spindle in machinery, such as CNC (Computer Numerical Control) machines.
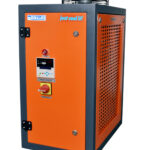
Refrigerated Air Dryer
Refrigerated Air Dryer is a type of device used in compressed air systems to reduce the moisture content of the air. It operates by cooling the compressed air to a temperature where water vapor condenses into liquid water.
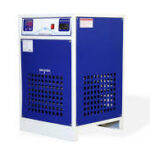